I worked the rigs from three to midnight, On the Corpus Christi bay
I'd get off and drink 'til daylight, Sleep the morning away
I had a plan to take my wages, Leave the rigs behind for good
But that life, it is contagious, And it gets down in your blood (Robert Earl Keen)
Following on from our previous article, we continue this week’s Texas theme with a deeper dive into some of the driving trends in oil and gas production across the great state. While the Drake well in Pennsylvania takes credit for the first real oil production in the US, Texas basins have long held the mantle of the top producers and have driven much of the innovation and technological progress for hydrocarbon production.
A key area of progress for the industry is the increased sensing/perception of production and the automation of the many assets across the basin. The large geographic spread of the wells and connecting infrastructure, coupled with the remoteness, creates unique challenges for acquiring good quality data and information from the field…and then appropriately applying insights gained back to the assets in an efficient way.
These puzzle pieces are extremely important for Pontem Analytics as we look to leverage the available and good quality data, together with our industry-leading domain expertise in process optimization and production chemistry, to develop value-adding insights, tools and solutions for the onshore industry.
The growth and accessibility of wireless sensors, remote communications (like SpaceX Starlink), and edge devices provide a hardware and infrastructure foundation for the utilization of advanced analytics and machine learning techniques to deliver unique insights to these operations which are always chasing margin.
Interview with Coby Fontenot, Automation-X
We recently caught up with Coby Fontenot, Regional Business Manager with Automation-X to discuss his experience and observations across Texas.
What do you see as the biggest challenges facing the Eagle Ford over the next 12-18 months?
Competition for human talent. There are hundreds of opportunities in the Permian Basin for young and aspiring technicians, management, and engineers, and in many cases, paying larger salaries. There is also a generational gap in the liquid and gas measurement world, as well as in the Automation/-I/E space. There is a large group of retirement age folks looking to exit the workforce that have held these positions for years that are now between 60-70 years of age. Then there was somewhat of a generational gap because the majority of that generation of employees were very loyal to the job & company and vice versa. Now a very large group of “senior” employees are only between 37-50 years of age. So, there is a 10 year gap in experience. This can be both counterproductive and unsafe.
There’s a lot of know-how that gets picked up just by doing it! This is something that has been developing for quite some time, actually. Talking with most operators and “The great crew change” is a very real issue facing the industry. Nobody is going to solve a 10-year experience gap over the next year and a half. However, processes can be buttoned-up, developed, automated, ‘codified’, and trained on to minimize the downfall.
How do you see automation playing a role in improving efficiency / utilization across the basin?
Automation is, and will continue, playing an enormous role in efficiency and utilization. The younger generations have really great visions and ideas on the continuous evolution of oil and gas automation and SCADA systems. The sophistication of today’s and future systems will continue to optimize well production and longevity, and continue to decrease downtime and loss production. On-site surveillance and fugitive emissions cameras are also becoming a critical component of today’s systems. These systems increase production, while decreasing the amount of man-hours, drive time, fuel expense, truck maintenance, and even reduce the risk of exposure to the hazards that cause on-site injuries.
When wells are remote, it is critical to understand tank sizes and chemical injection rates. The advancements in remote tank level tools has made it possible to optimize chemical delivery runs. We spoke earlier this week about treater truck delivery optimization (https://news.pontemanalytics.com/p/texas-projects-update), however on the opposite end, if a chemical tank runs empty it could mean shutting in the well (worst case) or operating sub-optimally at best. Automated data also helps reduce employee HSE exposure risks.
At Pontem, we have seen the need for automation first-hand in many of the problems we help address for our clients. As an example, when trying to optimize pigging operations in a midstream network, we have struggled with reconciling the planned pigging schedule vs. what is actually done…or, sometimes even worse, what personnel in the field write down. Automation in terms of data entry, fed from pig sensors, would help not just to ensure a single source of truth, but it would free up time/effort from people on the ground that already have an ever growing list of responsibilities.
How are you combining automation with analytics to drive CAPEX or OPEX down?
The automation and SCADA systems bring in tons of priceless data to the production engineers. The data can be trended and analyzed to prevent future equipment failures. This can contribute to lower CAPEX on a new well pad knowing what equipment worked the best in the past and help keep optimal production. That same data can also tell us what equipment might fail at what critical point in its lifespan so that we can perform preventative maintenance to reduce downtime, thus reducing OPEX. This is very critical to Automation equipment providers like myself.
Hearing Coby say this was like preachin’ to the choir. We’ve been on both sides of the story. It feels much better talking about leading / lagging indicators for a potential problem than to be out in the field running a Root Cause Failure Analysis using ILI analyses on a cut-out spool that has a corrosion failure. Knowing there were elevated risks of corrosion would have allowed operations to introduce chemical or mechanical (pigging) mitigation programs as part of the Integrity Management (IM) program.
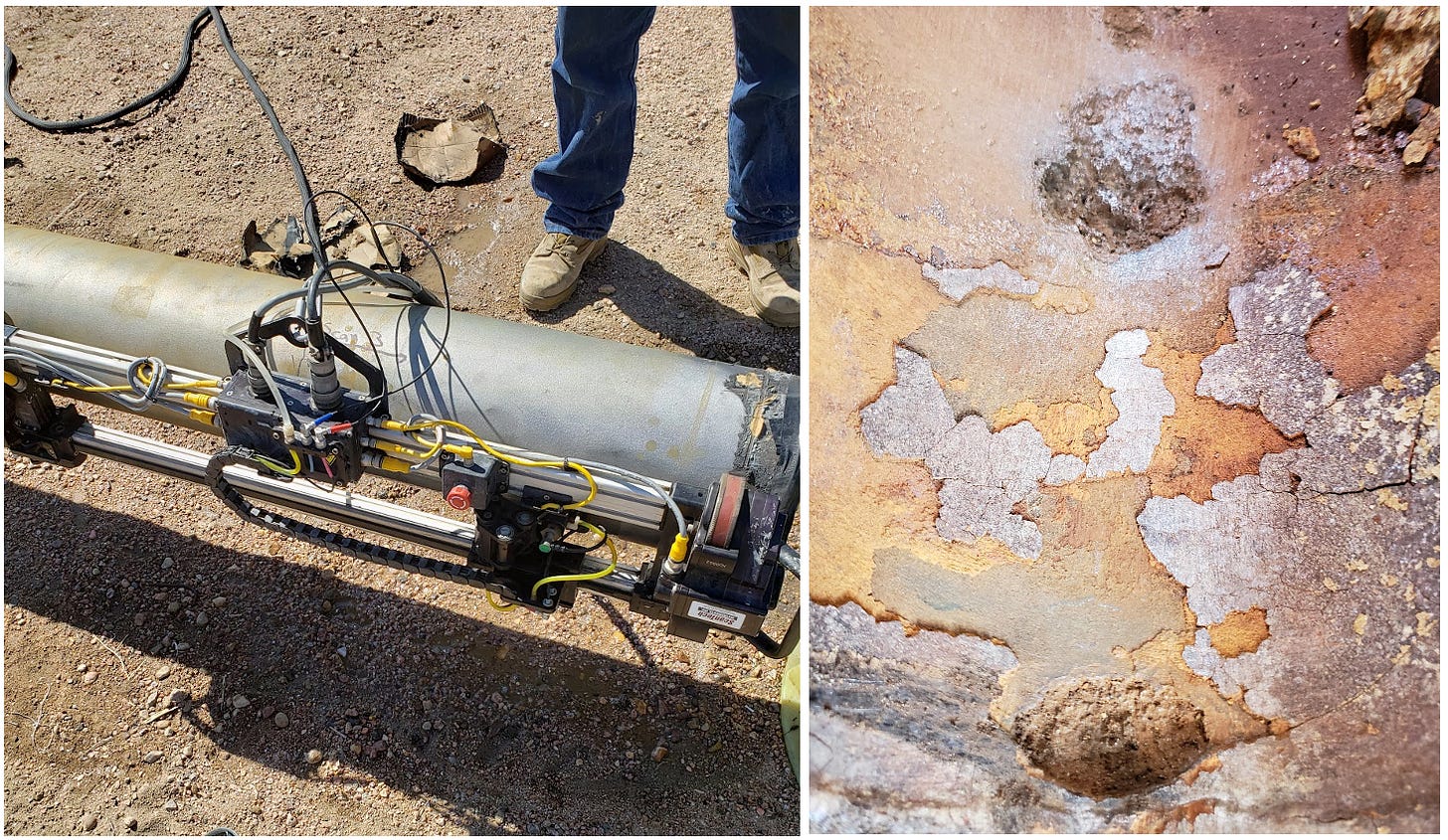
What is your outlook for the future of So Texas / Eagle Ford over the next 3-5 years?
I have been in the liquid and gas measurement and Automation-I/E field service, design, and product sales and support for 18 years, with 12 of them being in the Eagle Ford. It has peaked, slowed, rose again, and now seems to be very stable and sustainable for the foreseeable future. The infrastructure was built early on, and has continued to be updated and grown from increased pipeline capacity to overhead AC power being supplied to even the most remote locations. I believe that the different variations of Artificial Lift and Re-Frac technologies will also play a huge role in increasing the life expectancy of the Eagle Ford wells.
We couldn’t agree more with Cody. Working smarter with advanced data collection and processing will extend the life expectancy of wells and allow for work-overs and life extending techniques such as artificial lift more effective.
In speaking with some of the operators we work closely with, refrac technologies is definitely a hot topic. Some are starting to swear by it’s potential, while others are leaving the jury out while they continue to evaluate it. Hearing about the ‘next best thing’ in production isn’t new, so many are cautious before calling it a holy grail. Nevertheless, discussions, analyses, and papers are ramping up.
Wrapping up
While there are obvious challenges, we see an incredibly bright future for Texas. There is a massive opportunity to leverage the deep history and wildcatter attitude of Texas together with the latest in automation and digital approaches from around the world to deliver the next generation of energy for this great state. It’s easy to say “let’s do it all!!” but very difficult to put it all together. If that’s something you’re chasing then you’ve come to the right place… drop us a line and we’ll steer you in the right direction!