Last year, we spoke about hydrate mitigation strategies and shared some beautifully-captured lab pictures. There was a deep-dive into hydrate inhibitor selection methodology, particularly related to low dosage hydrate inhibitors (LDHIs) as an alternative to a CAPEX-intensive MEG unit. We touched on some ongoing / novel work in this space, promising to come back and finish the story when we were ready to talk about it.
Thirst Traps and SuperTRAPP
When done correctly, chemistry tells a beautiful story through pictures. #nofilter. In this week’s installment of Data and Discipline, we tackle a challenge that the offshore industry has dealt with for many years and hope to shed some light on the decision-making process that goes into some…
Well, after 4 months, we are finally ready to talk again. Hopefully, we didn’t keep you waiting - 4 months isn’t *that* long if you have a good story. We matured (the work) during our (hydrate crystal) growth era. And we failed. A lot. Often in fantastic fashion. We almost gave up hope it would work out. Key word being almost. As Babe Ruth once said - “It’s hard to beat a person who never gives up”. We kept at it over the last few months, in hopes there may be a happy ending to share. And, don’t worry - we didn’t forget to take a few seductive (hydrate) pictures along the way.
We again enlisted KAT Labs (UK) to assist with the heavy lifting of running the tests and their photography skills. Amazing job by Neil and his team.
Technical Challenge (Review)
The original problem was looking at alternatives to a traditional mono-ethylene glycol (MEG) regeneration / reclamation unit (MRU) for hydrate control of a deepwater gas development. Hydrate conditions were pretty standard, with ambient temperatures of ~4°C (40°F), sII hydrate structure, and high sub-cooling (>10°C).
We knew MEG would work (technically), but the up-front CAPEX was a challenge for the project economics. So, consideration for alternatives - namely anti-agglomerant low dosage hydrate inhibitors (AA-LDHI) were evaluated. The unique technical aspect was the low liquid loading of the gas/condensate reservoir fluid, making the use of anti-agglomerant chemistry questionable from the outset. But, we like a challenge…
At this stage, we were looking at proof-of-concept only: Is there a chemical available on the market that meets the technical criteria?
Additionally, and what would prove to be one of the key challenges for the evaluation, was the ability to get a representative test to mimic field conditions.
While not exclusive, by and large laboratory hydrate testing is conducted using isocratic methods. This method offers a very convenient measure of hydrate formation onset, and an indirect measurement for hydrate conversion. Because the volume of a given hydrate fraction is significantly less than the gas and water that composes the hydrate structure, simply putting a pressure transducer on the cell allows one to see a deviation in the linear pressure/temperature relationship. And the more hydrates that form, the larger the dP drop.
The drawback? There is a finite volume of gas to make hydrates. So, during the test design phase, one needs to be aware of the GLR (gas to liquid ratio) so the system is not inherently gas starved and hydrates don’t form! It turns out for most cases, a 50% liquid loading a reasonable default: high GLR to allow for the possibility of 100% conversion of the aqueous phase and there is enough liquid phase to visually see hydrate forming and observe large pressure drops. It most certainly allows us to screen options between different candidate chemistries, which is where a lot of the testing application usually rests.
The liquid loading is definitely tunable though. We have worked on a number of projects that were at risk for hydrate plug formation, and this was demonstrated in hydrate models and under “standard” laboratory test conditions. However, when we accounted for the actual expected GLR, the system is gas starved and hydrate plugs were impossible to form under actual field conditions. It turned out even 100% conversion of the gas did not create hydrate volumes sufficiently large enough to deposit and plug. It is challenging when your test - to prove field applicability - is not always a reliable predictor to field scale-up.
But what about the other way? How low could liquid volumes go and still be viable for AA-LDHI treatment. A general rule of thumb often stated is water cuts <10% can’t be reliably evaluated in rocking cells because there isn’t enough hydrate volume to stop the ball and plug the cell (or the hydrate forms at the edge of the cell where it can’t stop the ball). Similarly, autoclave minimum water cuts range 2-4% depending on the system and how responsive the torque measurements are. This is where we needed to stress-test our application in this case study.
Testing Limit: Water Cut or Total Volume
When presented this this technical challenge, we asked ourselves if this is due to the water cut or the total volume? In other words, if we had the same total water volume but a higher water cut, could we get pass/fail differentiation? We also conducted a brief industry survey for highest GLR systems successfully treated with AA-LDHI’s. It turns out the liquid loading conversion looked to be ~7-10% for known field applications. So, could the same be applied to the lab test conditions, which offered some hope that a direct scale-up was possible.
Green Chemistry?
If the conditions weren’t already challenging enough, another carrot for the project team was to demonstrate feasibility with a “green AA-LDHI”. The poor reputation of AA-LDHI technology environmental profile has prevented their applications in certain regions, so it is worth considering green technology. Biodegradation and bioaccumulation are two areas in the chemical biotoxicity profile in which AA-LDHI’s struggle. Most chemical service companies have active research to develop a green AA-LDHI, and in all honesty have made significant strides with “not-quite-green yet” new chemistries.
Put simply, the traditional chemical scaffolds responsible for the exceptional performance are also a reason why they have lackluster profiles in biodegradation and bioaccumulation categories. While improvements are constantly coming, the known drop in performance between green and non-green AA-LDHI prevented us from considering green chemistries at this early stage. Especially, in the midst of a proof-of-concept study to determine if AA-LDHI could possibly perform under extremely challenging conditions.
Testing: Low Liquid Loading
Initial testing was done at low cell loadings (10-20%), mainly as an attempt to get a repeatable test that could be used for decision making. Could the test actually identify hydrate formation and agglomeration in a repeatable pattern? We not only need to “see” hydrate formation (or not), but need to be able to take actions on the variable impacts (liquid loading, water cut, etc.). Below is the first inhibited test (using deionized water, DI).
Initially, two distinct layers are observed (lower = LDHI-dosed water, which is opaque/milky. upper = condensate)
During cooling period, two layers are observed with evidence of small, discrete hydrate crystals along inner cell surface)
Nearing end of cooling period, hydrate slurry forming. Uniform appearance, with significant areas of hydrates along inner cell surface)
At end of cooling period, hydrate plug has formed with ball bearing stuck in hydrate crystal layer
4 different LDHIs (from 4 different vendors) were selected for evaluation. The tests were repeated, as well as running multiple “blank” (no LDHI) tests. They all failed at slightly different times during the cooling period of the test. The inhibitors offered some slight improvement over the blank, but all of them still failed very early. Nothing like consistency and repeatability. And being a total failure.
Since we were looking at stretching the limits of low liquid loadings within the rocking cell, it was difficult to determine whether the tests failed due to (a) poor chemistry (unlikely, these were all field-proven applications), (b) unreasonable test parameters (unlikely, these were pretty standard requirements), or (c) unreasonably low experimental test conditions. To address the later, the decision was made to increase the loading. Important to note that the initial low liquid loading tests were already at/above the expected field conditions (~5%). Increasing the loading above 10-20% in order to find the passable limit was nice (experimentally), but immediately introduced questions related to field scale-up IF we found a pass.
Low-ish Liquid Loading
Liquid loading in the cell was increased by 2-3x (over the original cases). While the absolute value of liquid in the cell remained small (on a cc-basis), the relative gas/liquid ratio is now well-above the expected field condition. But as the testing was stretching the lower limit of liquid loading, it was prudent to know if this would yield a pass, thereby differentiating the impact of liquid holdup on test results (pass/fail).
The testing showed an immediate improvement in the delay of hydrate blockage. Hydrates were no longer forming during the initial induction (cooling) period and were able to persist for longer. However, ultimately, the all still failed and formed hydrate blockages in the cell.
AA-LDHI’s operate by preventing large hydrate agglomerates from forming and dispersing the small crystals into the hydrocarbon phase. As more hydrocarbon volume is available, the more suitable the system is to transport significant solids volume. As mentioned earlier, hydrate volume is less than the equivalent gas/water volume. So, increasing the total liquid in a closed system (i.e., maintaining the same water cut) improves transportability.
We observed the increase in liquid volume as sufficient to survive the initial hydrate formation during the cooldown phase. However, during the steady-state phase, hydrate networks can continue to grow especially if there is limited hydrocarbon to disperse them. And, in fact, we observed a gradual thickening of the hydrate slurry, followed by eventual plugging.
Testing Crossroads
Up to this point, tests were run at conditions which a pass was expected. The LDHIs selected (and dosages) were all within reasonable application ranges. Even after increasing the liquid holdup beyond field conditions, there was no valid pass. Several questions emerged:
Do we have a valid testing program with the low liquid loadings used in the rocking cell? Perhaps low liquid loading testing is just not practical for AA evaluation.
Is there something wrong with the test equipment? Is a rocking cell just the wrong equipment to use?
Did we just pick 4 bad chemistries (from 4 separate vendors)? Did we just pick poorly on our LDHI ‘speed dating’ criteria and would 5th time be the charm?
Are the assumptions around critical water cut wrong? Do we have a much lower tolerance for water cut threshold in this system?
Is there something unique about the formation water chemistry (it is quite low, which makes AA application challenging)?
Is there something unique about the condensate liquid phase being tested (is it just a super-spreader for hydrate agglomeration)?
Water Chemistry (DI → Formation)
AA-LDHI chemistries are surface active molecules, containing a hydrophilic head-group and a hydrophobic tail (ironically resembling lipids found in many biosystems…see green chemistry above). The surface structure of hydrates is polar, and remembering our basic solutions chemistry, “likes dissolve likes,” one generally accepted mechanism is AA-LDHI’s will associate the polar head group with the hydrate surface. Similarly, the hydrophobic tail associates with the hydrocarbon phase and helps to disperse the hydrates into the oil phase. Increased salinity in brine is known to improve AA-LDHI performance by improving the chemical’s ability to disperse hydrates into the crude oil.
The TDS was increased from DI to moderately saline (slightly higher than seawater, which is ~35,000 mg/L). We were aware salinity will decrease subcooling, and the intent was to minimize any change in difficulty from a thermodynamic standpoint. We also recognized the field in question would have low to no salinity, however we wanted to relax some of the constraints in the design of the test. As noted below, we do see some improvement with the introduction of salinity to the system. Ultimately, however, we see a hydrate plug and the inhibitor is not able to overcome the system. While the salinity tested is still considered “low,” there are several known field applications for AA-LDHI chemistries with salinities ranging 10,000 - 35,000 mg/L. In other words, condensed water systems are incredibly challenging for AA-LDHI’s. By introducing *some* salts to the conditions, we have backed in another parameter in which AA-LDHI’s are known to perform.
Decreased Water Cut
In looking at other levers to pull in order to find the AA-LDHI performance envelop under wet gas condensate conditions, we turned to decreasing water cut. A system water cut is probably the largest dependent variable for AA-LDHI chemistries. For cutting edge AA-LDHI technology, water cuts are the “how much you bench?” metric: how much water can you treat?
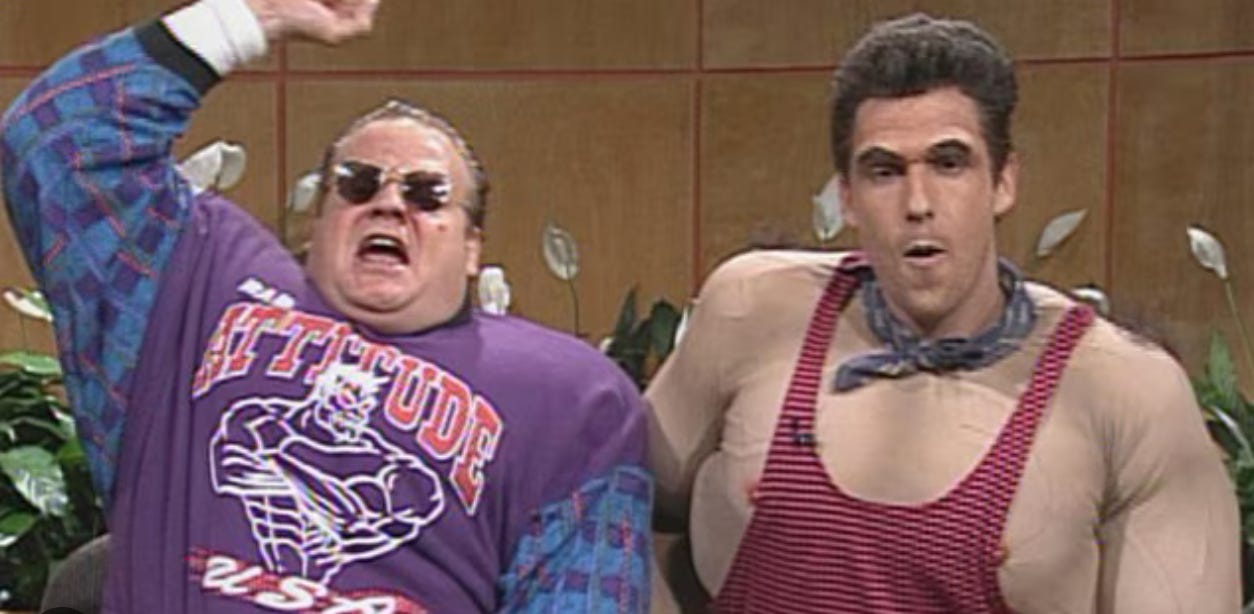
To this point, we had purposefully used moderate to higher water cuts because we were concerned with maintaining enough total aqueous volume to avoid a false negative result. As we had increased total liquid loading, we felt decreasing water cuts would not cause false negatives. Additionally, life of field estimates allowed us to reduce the water cut and still be within the project scope. So, how’d that go for us?
Again, we continue to see improved performance trends, and we expected the lower water cuts to be easier for the LDHI to perform. The decrease in water volume (and hence hydrate volume) has placed less strain on AA-LDHI performance, however we still observed hydrate plugging in the steady-state phase of the test.
More Liquid Loading
At this point, the mad scientists are pulling whatever hair is left on our heads. We have slowly eased many of the performance variables into realms of known performance. There were only a few more things left until we were back to a “regular old cracker” AA-LDHI test (look up Eddie Murphy jokes). We were determined to get a pass. We decided to ease in more liquid loading to see if we were still beyond a viable performance envelop.
We again increased liquid loading, which dramatically improved the inhibitor performance. Note, the AA-LDHI was able to inhibit a hydrate plug through the steady-state, shut-in, and survive the initial restart phase. So, what happened? Again, additional hydrocarbon phase volume is available to transport and disperse the hydrate slurry. While we saw a small bump in inhibition time the first time liquid loading was increased, we had since relaxed several other constraints. Here, additional liquid loading is added, there is a step-change in inhibition time, which nearly brought us to a pass. During the shut-in, there is no shear occurring to the fluids and there is an opportunity for the hydrate network to increase. The AA-LDHI was able to prevent a plug initially, however as the restart progressed a noted increase in viscosity steadily degraded the performance until an ultimate plug occurred.
Testing Crossroads II: Decision (and Budget) Time
While we can see that we are inching closer to a ‘pass’ result, this isn’t a PhD-level research project. Time and budget constraints put the work at a cross-roads::
Your next test (or 2) better yield a ‘pass’. Chose wisely.
Stop the project and be unable to answer the question of whether an LDHI would be suitable. Since we did not have a ‘pass’ at any condition, the entire testing approach and methodology remained an outstanding question at this stage. Could we effectively kill the LDHI option for the field OR had the whole testing approach been flawed from the start?
Holding the other variables constant - those that allowed us to get closer and closer to a passing criteria - we agreed to run two more tests, focusing on the following variables:
Water Salinity: As we were still quite low in total dissolved solids (TDS), the decision was made to increase salinity further. Again, this brought us further away from the project’s expected formation water chemistry, but given that water samples are inherently uncertain, it was not completely unreasonable.
It is well known that increasing salinities of a system will increase the surface tension and decrease emulsion stability. This same phenomena may help force the AA-LDHI structure such that the polar head group is more accessible to newly formed hydrates, which are developing at the water-oil interface.
Liquid Type: Most of the AA applications are for oil-dominated systems, so questions were raised about whether the condensate being used was leading to the failures. An oil was considered for the final test, which obviously does not represent the expected liquid properties for the reservoir in question, but was necessary to attempt and isolate that variable.
Black oils are known to be easier to treat for hydrates compared to condensates. Similarly to the increased brine scenario, black oils contain many more components including surfactants, which are thought to help disperse hydrates into the hydrocarbon phase.
Finally - a pass. Actually, TWO passes. A step-by-step process of adjusting variables did finally reach a passable test by end of the proof-of-concept phase. An LDHI *could* pass…but, at the cost of:
Liquid holdup increased beyond field estimates
Water cut increased beyond field estimates
Water salinity increased beyond field estimates
Liquid properties changed from field estimates
From the outset, it was an ambitious goal with a number of forces working against getting a passable test. The LDHI candidate for this application probably is not the right fit, given what we know. But, we do have a better understanding of why that is the case (rather than just relying on ‘gut-feel’ or outdated ‘rules-of-thumb’).
So now what?
What did we learn from the study? Well, depending on your frame of reference, a lot:
We can get reasonably good test sensitivity in the rocking cells down to <20% liquid loading, which is below what is typically used and offers some opportunity to extend the range of applicability of the tests. However, we are still left with the question of will a low liquid loaded test EVER pass? We did not go back and recycle those tests at higher salinity and/or different liquid phase. That would be interesting work to do. Maybe a Phase III to this story?
While we knew variables such as water salinity and liquid ‘type’ (condensate vs. oil, paraffin and/or surfactant impacts) would impact hydrate slurry behavior, we were able to delineate the impact on pass/fail testing criteria. There is nuance in applicability that often gets lost when we look for project analogues, as we need to consider all of these small, but important variables. Too often, we focus on the wrong traits when trying to find that perfect match. The small details matter.
The ‘scale-up’ problem in translating these laboratory tests into field application is a real concern. Given the low volume sensitivity of the testing carried out here, would that be applicable in large-diameter pipelines? And, is that a risk any operator is willing to take, particularly given the criticality of gas supply contracts? The size of the prize is substantial if we can eliminate the CAPEX-intensive MRU…but the cost of failure is equally (if not more) substantial.
The visual rocking cells give us a great opportunity to capture some amazing images. Having the numerical test data is very useful, but “a picture is worth a 1000 words” didn’t become a to be a cliche for nothing.
We will keep putting in the technical work to further push the limits of non-MEG field development solutions. The prize is worth the effort. Oh, and we will keep snapping and posting pictures…
Parting Thought
Given this story is going out right before Valentine’s Day (14-Feb) and I am spending it in Africa, we can use the lyrics to Disney’s Tarzan “You’ll Be In My Heart” to bid adieu to this hydrate case study:
For one so small, You seem so strong
Well, our hydrate crystal was not that small, being sII-type and not the smaller, methane-driven sI-type. So, we thought we had a chance…
My arms will hold you, Keep you safe and warm
Too bad, this development was deepwater and long-distance, so we couldn’t keep you warm at all…
This bond between us, Can’t be broken
That was the whole point of the LDHI option – we just want to modify the hydrate crystal agglomeration, not work on breaking the (hydrate) bonds. We just didn’t have enough liquid present to effectively disperse all of the hydrates.
I will be here, Don’t you cry
We have an answer that works (MEG), just not the one we had hoped for (LDHI). That should still work to prevent hydrates from forming, so no need for operations to cry.
‘Cause you’ll be in my heart…From this day on, Now and forever more
Now that we have a little taste of victory with the LDHI testing and better understanding some of the variables, we will keep working on getting those non-MEG options to work. The need for a viable alternatives still remain and the answer may very well lie within the LDHI chemistries available, today or in the near future.