If you have siblings, I am sure there were Battle Royal events for control of the TV remote. One time slot I fought a little harder for if we could get home from church on time was Sunday 11AM. All American Wrestling hosted by Mean Gene Okerlund was my go-to to catch up on all the week’s action. If you missed the glorious evolution of professional wrestling, and I’ll admit there has been a lot to keep track of, you may have heard of Raw or the massive WrestleMania events. One show that has stood the test of time, and is still going strong: Smack Down!!
I was reminded of Smack Down when a comparably larger-than-life development was recently in the news: the Smackover Formation. Spanning over 5 states, the Smackover Formation has contributed to the US conventional oil economy since 1922 with the discovery of the Smackover field in Arkansas. Since the initial discovery of oil, the production profile and characteristics have reached mature status: over 1,000 wells drilled in approximately 600 former and currently producing oil and gas fields, with ~150 of those fields in Arkansas. While there is still good production from the Smackover, it is no longer newsworthy compared to the vast reserves found in the neighboring US basins and/or produced offshore. But the sun is still shining and Arkansas is still making hay in the Smackover…
Beyond oil production, the Smackover Formation has been critical for the Arkansas economy for several generations through extraction of another resource. Did you know Arkansas is the second leading producer of bromine, which is recovered from produced brines in the oil patch prior to reinjection? In other words, Arkansas has found and developed a profitable and useful product from a “waste” stream in oil and gas production. The brine produced alongside hydrocarbons is rich in bromine, which is extracted, and the remaining bromine-depleted brine is re-injected back into the Smackover Formation. Bromine is used in fire retardants, agriculture, pharmaceuticals, and to make certain drilling fluids. All this to say Arkansas has a lot of unique, local knowledge with brine extraction processes, which can be applied in new and exciting opportunities.
This brings me to the point: Arkansas is potentially poised to provide another critical resource, as several production wells are also rich in another element: lithium (Li). Several brine deposits contain over 300 mg/L lithium in the composition. Compared to the Mason-Dixon Line of 80 mg/L concentration limits for profitability, the Smackover Formation sounds like an ideal location for lithium extraction!
A few months ago, ExxonMobil announced plans to become a leading producer of lithium, a critical metal for EV batteries. Phase 1 of the project has begun on the 120,000 gross acreage ExxonMobil acquired in the Smackover Formation in early 2023. You might be asking, “How in the world is Exxon going to successfully produce lithium?! Aren’t they an oil company and not a mining company?” I’ll come back to this, as Exxon’s oil exploration experience will greatly add to their chances of success.

This is welcome news given the smack down the US has taken over the last 30 years on the lithium mining front. Back when I was hanging on Mean Gene’s every interview in the 1990’s the US was the largest producer of lithium. As Macho Man knew, it’s good to be the king…
How times change! My friend and colleague Conor Sherrard noted recently in a post (https://news.pontemanalytics.com/p/gday-mate), Australia now accounts for 50% of global lithium production. In fact, 90% of Li production comes from just 3 countries (Chile and China being the other two). The only active lithium mine in North America is in Silver Peak, Nevada, where lithium brine extraction started in 1966. The lithium occurs in an infilled playa sequence that covers an area of 72 km2 within a closed drainage basin of 1,342 km2 (Munk et al. 2011). Average lithium content at the initiation of production was 360 ppm in 1966, declining to 230 ppm in 2008 (Garrett 2004). The mine currently produces 3,500 tonnes of LCE per year, with the capability to produce 6,000 tonnes of LCE per year.
You may have guessed, the biggest increase in demand for lithium has been the push towards renewable energy, which requires batteries for energy storage and eventual utilization of the energy harnessed. Whether it’s oil, gas or renewables, it’s critical the US achieves energy independence. We’ll get into where the lithium is coming from, and I’m going to go out on a limb and state you have probably heard the majority of lithium processing from hard rock is concentrated in plants located in China. That begs the question: does the US have resources to support domestic demand?
There is the Thacker Pass Lithium Mine expected to add to the lithium footprint. Additional domestic mines under consideration also include further development in established lithium mines in North Carolina. The Salton Sea in California has been in recent headlines after Controlled Thermal Resources Holdings Inc., broke ground in January on a $1.85 billion project to construct a fully integrated lithium and renewable power production facility. The Salton Sea already has environmentally friendly geothermal power plants and the new lithium project is set to become the first to combine a geothermal power plant with lithium production. At full production, the plans call for an estimated 300,000 Mt Lithium Carbonate Equivalents, or LCE, annually. While the reserves sound promising, harvesting from the Salton Sea has thus far proven to be difficult. Berkshire Hathaway Energy has been involved in the Salton Sea for quite some time. And on the lithium extraction front, the California Energy Commission gave a $6 million grant to Berkshire Hathaway Energy (as well as a $1.46 million grant to Controlled Thermal Resources in 2020). The U.S. Energy Department awarded BHE a $15 million federal grant in 2021, but the grant was rescinded due to “material changes” to its project. That isn’t meant as a slight towards BHE. It’s an acknowledgment this isn’t easy! There is a reason EV battery grade lithium predominantly comes from hard rock. Which is why having ExxonMobil jump into the fray is welcome news for domestic security on the renewables energy front.
These expected reserves and timelines to develop new sources of lithium still puts the US behind the curve for EV battery supplies and haven’t thus far shown themselves to be viable solutions to achieve renewable energy independence, at least in the short term. Are we over a barrel (no pun intended)?
If you want to get down, you gotta get to Arkansas…
Chris Stapleton
From 2010 to 2021, lithium demand for batteries rose from 23% to 74% of total lithium consumption. And demand is only going up, exponentially in some estimates. One usable form of lithium in EV batteries is lithium carbonate (Li2CO3), and most references will reference Lithium Carbonate Equivalents (LCE) when talking about supply / demand. So, the ~106,000 tonnes of Li produced in 2021 equates to 540,000 tonnes LCE. By 2030, demand estimates range 2 - 3 Mt: a 4 - 6x increase in a short period of time!
Let’s take a quick look at how quickly those numbers have stacked up. Perhaps surprisingly, there have been somewhat contentious debates on how much lithium actually goes into an EV battery. It seems the true amount of Li in a battery isn’t clearly reported by manufacturers. Don’t worry, I’m not about to jump into that Royal Rumble. If you’re interested in the number crunching, Paul Martin has an interesting 2017 LinkedIn post (https://www.linkedin.com/pulse/how-much-lithium-li-ion-vehicle-battery-paul-martin/) and he lands on 160 g Li metal per kWh of battery power (~850 g LCE). If a typical EV battery has 50 kWh capacity, this equates to 40 kg LCE per battery and if one assumes 40 million vehicles projected on the road in 2030 (at 50 kWh/vehicle), that puts us at 1.7 Mt LCE.
So, is there enough Li supply to support the increasing demand for EV technology? Maybe. Based on projected EV demand, some estimates show ~40,000 to 60,000 tonnes LCE shortfall in 2025. Below are projected LCE production levels by country and by source (more on the sources below).
While most experts will agree the reserves are there to support global demand long term, there may be regional shortages and intermittent delays in the near term. The delays are attributed to the time required for a discovery mine to be developed. To frame the concern in one way, consider the development from first discovery to full operation: developing a lithium mine can take as long as 10 years. There are currently 101 lithium mines in operation, which are a mix of igneous and sedimentary deposits. The most widely accepted estimates report approximately 28 Mt Li are within the known worldwide deposits.
That sounds like a lot of lithium! What’s the problem? Some of the issues are related to process specifications and not all lithium is created equally! You didn’t think you could get away from Quality Control that easily, did you? There are some consistencies producers and battery manufacturers have regarding some purity specs. For example, iron (Fe), aluminum (Al), lead (Pb), and zinc (Zn) are tightly controlled, as these metals are particularly deleterious in battery manufacturing processes. However, other contaminants are less consistent. Chloride contamination tolerances can range 10x! Sodium and sulfate specifications can range 150 - 650 ppm. This presents a problem gaining agreement between lithium producers and battery manufacturers, and while manufacturers are not single sourced in their supply, bringing on a new source is time consuming and arduous.
From lithium deposits harnessed from hard rock, Spodumene (LiAlSi2O6) is the most valuable lithium containing mineral as it contains the highest concentration of lithium. Good quality hard rock will contain a couple percent coming out of the mine and after an initial processing cut increases to roughly 6-7% Li2O equivalents. Spodumene occurs naturally in an α-monoclinic crystal structure, which is one of seven known crystal structures. It can be described by vectors of unequal length: two vector pairs running perpendicular and a third pair makes an angle other than 90˚.
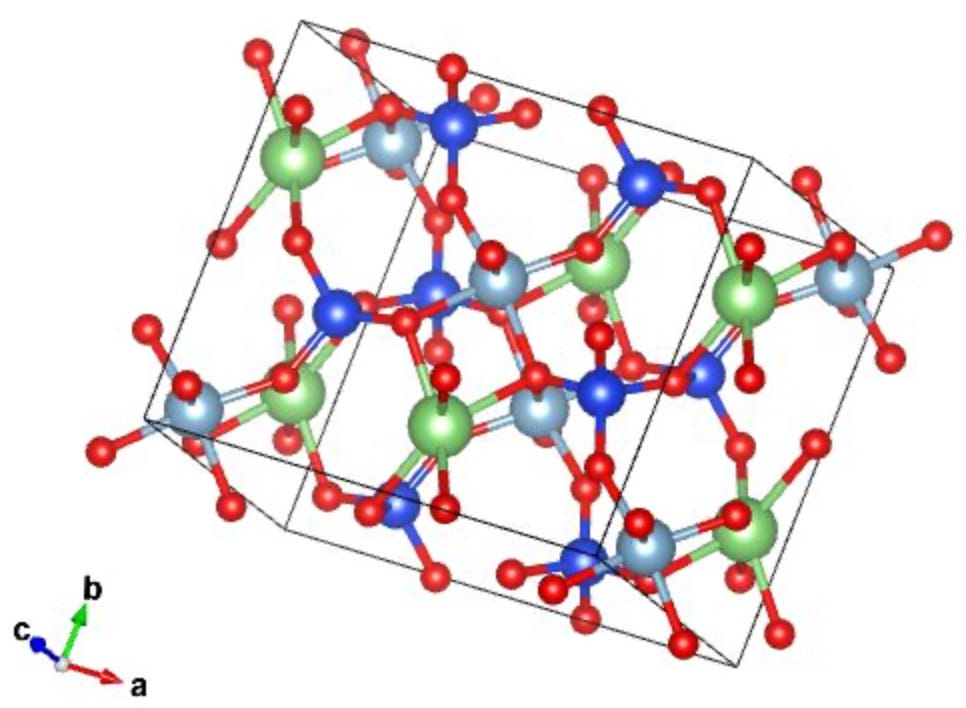
This particular structure is compact and resists chemical attack. In other words, pulling lithium out of spodumene is incredibly difficult because the mineral’s molecular geometry protects lithium from extraction. To prepare the mineral for reaction, it is heated and pulverized into a fine powder. The next steps are challenging enough that they are done at secondary facilities away from the mining operations. This is why Australia stands atop the production list for lithium ore production, yet the majority of lithium processing is done in China. In fact, 80% of the raw materials for advanced battery manufacturing come from China. The process is intensive and expensive.
The first chemical reaction step is to transform the spodumene crystal structure from α-monoclinic to the β-form, which has a tetragonal crystal structure. The more reactive crystal structure is formed by stretching one of the cubic lattices along its lattice vectors such that the cube becomes a rectangular prism. The lithium metal extraction requires this transformation, which is thermally intensive: temperatures in excess of 1,000˚C are required to overcome the activation energy to change the crystal shape. The second step is an acidic extraction process using sulfuric acid and additional high temperatures.
2 LiAlSi2O6 (𝑠)+ H2SO4 (𝑙) →2 HAlSi2O6 (𝑠)+Li2SO4(𝑠)
The lithium sulfate is leached with water and is further reacted to the final product. For high purity grade EV battery products, this is lithium carbonate or lithium hydroxide (we’ll refer to this simply as LCE). In the case of making LCE for EV batteries, sodium carbonate is used for the final transformation to lithium carbonate. This high energy and chemical intensive process equates to mining 8 tonnes of spodumene to produce 1 tonne LCE. All in, LCE costs from hard rock sources to final product are approximately USD 2,500/tLCE.
And what I found in the Ozark Mountains I ain’t ever seen
It sure does feel like you’re sittin’ on top of the world to me
So, what I’ve focused on to this point is a resource not prevalent in the US (hard rock sources) and processes that are energy intensive (aren’t we ultimately looking for renewable energy, and this seems counter to the point) and require environmentally unfriendly chemicals. That seems like a hard lift domestically. What other options are there?!
The other main source of lithium is brine extraction, with 31 Mt lithium estimates available. The majority of brine sources, unsurprisingly, come from oilfield brine. Brine reservoirs, also known as salars, for lithium extraction is predominantly produced in Chile, Bolivia, and Argentina. The predominant method for lithium extraction is through solar evaporation processes, which takes months to over a year in order to concentrate lithium and process into a usable product.
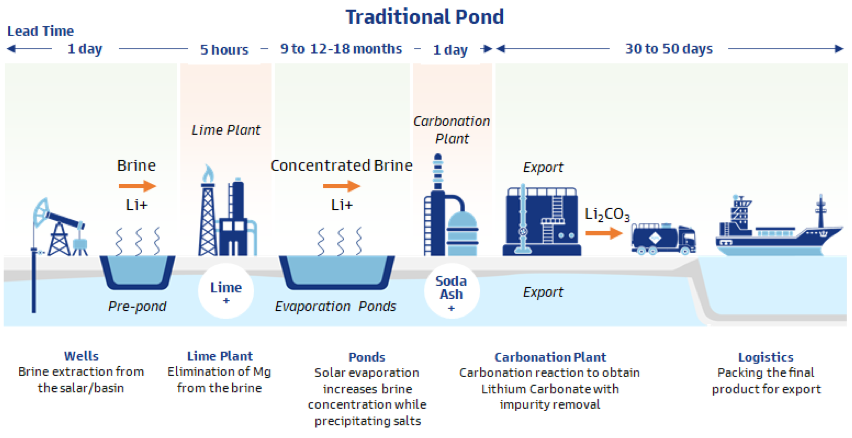
The average cost to produce lithium products via the traditional pond methods is USD 5,580/tLCE, which is significantly more expensive than cost estimates for hard rock production (USD 2,540/tLCE, source: S&P Global Market Intelligence, 2019). You might ask what is the incentive for brine extraction. The answer is an almost 2x margin advantage over hard-rock production. Unfortunately, as it stands now the majority of brine extracted lithium, which is produced in South America, is not battery-grade material. Lithium from these sources is utilized in other market segments. To change this, either additional processes must be put in place at the production sites for improved purity, or advances must be made to increase tolerance of the impurities. Neither is an easy fix.
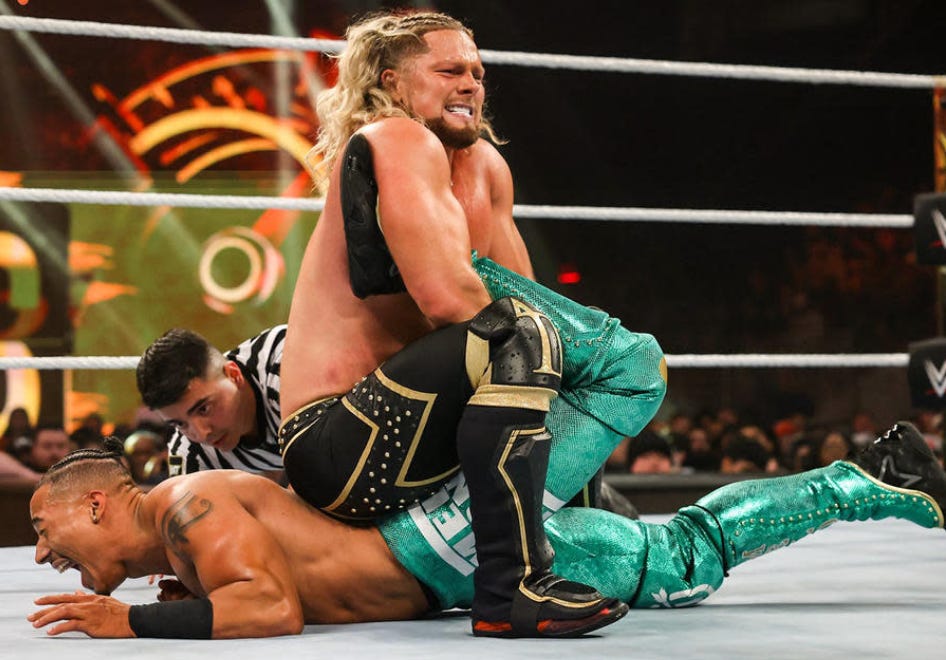
We have come full circle back to ExxonMobil and the Smackover formation, which is considered one of the most prolific lithium sources in North America. According to a press release from ExxonMobil, they will utilize direct lithium extraction (DLE) technology to separate lithium from the brine. The lithium will be further reacted to battery grade material, while the brine byproduct will be reinjected back into the formation. If that sounds familiar to you, the Smackover formation bromine extraction processes we mentioned earlier follows the same core concept:
Produce high brine content water
Extract desired mineral
Re-inject water back into the formation
DLE offers an innovative way to improve processing costs and purification specifications compared to traditional evaporation beds, which will allow brine lithium sources to be more easily utilized in EV batteries. Another feature with DLE is the smaller environmental footprint required. It takes less physical space, does not require energy intensive heating, and uses less harsh chemicals to extract lithium from the source.
Furthermore, the lithium production is a bolt-on to already existing processes, which means the 150 fields in Arkansas that are already producing and mature are more easily exploited for lithium production compared to a scenario requiring new drilling operations.
That sounds great, but what reserve estimates for lithium are there? Within the LANXESS lease parcels, Standard Lithium reports Measured and Indicated Resource of 2.8 Mt LCE at an average lithium concentrate of 148 mg/L; and Proven and Probable Reserves of 208 Kt LCE at an average concentration of 217 mg/L, (https://www.standardlithium.com/projects/arkansas-smackover). Remember, conventional estimates call for > 80 mg/L concentration to be viable…OK, I’m listening…Estimates state the first production plant scale up to yield annual production of 5,700 tonnes LCE, which exceeds the current Nevada production mentioned earlier (3,500 tonnes LCE).
According to the same publication, Standard Lithium has been operating an industrial-scale fully integrated direct lithium extraction (“DLE”) demonstration plant at the LANXESS South facility since May 2020. Standard Lithium claims the DLE process offers several advantages over traditional evaporation beds, such as a smaller environmental footprint, higher efficiencies, and a consistent overall purity. If you recall, the Smackover formation has been processing brines for a long time and are efficient at it! The new DLE process offers a seamless process to begin producing immediately.
Havin' so much fun that it's probably a little bit against the law
All the boys and the girls down there sure do know how to have a ball
So, what is the direct lithium extraction process? There are multiple techniques that are widely used in other industries and applications that are now being implemented in DLE facilities. The interesting and innovative part of it all, is the fact these techniques are proven technologies. If you’ve spent any time in a chemical or analytical lab, you may have used some or all of them. Some processes DLE may incorporate include,
Adsorption columns - the lithium salt (LiCl in most cases) is selectively captured by a sorbent material. This can either be accomplished in vessels with free floating sorbents, or on fixed-bed solid media. Both of which contain lithium-selective material to extract lithium from the brine. This is a versatile process allowing for a range of lithium concentrations. The downside of this process includes a high upfront cost and additional processing steps to convert the lithium to LCE.
Ion exchange - similar to adsorption columns, lithium is selectively extracted from brine by replacing the lithium with an alternative ion (sodium, for example). Again, higher upfront costs and requires a second conversation step prior to exporting.
Solvent extraction - lithium is extracted from brine into an organic (hydrocarbon) solvent. The process is efficient and has a low cost associated with it, however corrosion is a major concern in the processing and there is a large environmental impact with the use of hydrocarbon solvents.
Membrane separation - lithium-selective membranes are used to separate lithium / magnesium ions by an external driving force. This is an efficient and environmentally friendly process, however there are limitations, namely low sodium/potassium content brine. The technology comes with a high up-front cost.
Following extraction processes, further purification and concentration of the lithium salt solution, typically LiCl, produced by the DLE process uses chemical softening and impurity removal processes that are industry standard processes for water and wastewater treatment. These include, BWRO (Brackish Water Reverse Osmosis), lime soda softening, ion exchange for removal of calcium (Ca), magnesium (Mg), and boron (B), and OARO (Osmotically-Assisted Reverse Osmosis). None of these processes are as energy intensive or require harsh/harmful chemicals.
The final production step is the battery-quality lithium carbonate production step. Here, purified LiCl solution is reacted with sodium carbonate (Na2CO3), producing crude lithium carbonate. Interestingly, and importantly, the initial product contains impurities that would prevent application with EV batteries, and so there is a purification process in which lithium carbonate undergoes conversion to lithium bicarbonate, purified via ion exchange, converted back to lithium carbonate and crystallized to produce pure lithium carbonate. The final product is dried, milled, and packaged prior to shipping to a battery manufacturer. One obvious benefit is the fact the lithium is converted to battery-grade material onsite, as well as the faster process associated with DLE. To recap, we have another potential source of lithium right here in the US. The process to harvest and convert it to a usable resource does not require harsh conditions or chemicals. This is starting to sound like there’s something worth pursuing!
I noted earlier Exxon is in a unique position to capitalize on DLE from brines because of the similarities to traditional oil and gas exploration. As one of the largest publicly traded international energy and petrochemical companies, Exxon is well-versed in exploration, drilling, and extraction of fluids. Exxon has also committed itself to a holistic approach towards securing energy for our future in a wide-variety of sources. In other words, this doesn’t seem like lip service. The partnership with Arkansas is particularly exciting, as Arkansas is one of the few states with well-established production and brine extraction. The Arkansas brine-laws should offer an easy transition and avenue for producers wanting to operate in Arkansas and for other states wanting to attract local business for the development of lithium production.
Pontem (Li)nkage?
So, what does a data analytics company like Pontem care about Lithium? Well, a couple reasons:
Lithium resources have been identified in Zimbabwe, Namibia, Ghana, the Democratic Republic of Congo (DRC), Mali and Ethiopia. The continent has become a hotbed of activity to secure the coveted metal. China is already making inroads to extract lithium, with recent activity in Zimbabwe in particular, with over $1billion invested over last 2 years. Earlier, we already discussed the mature mining operations in Australia, and taken together, Pontem finds itself established and *smack down* in the middle of two regions with the some of the most prolific lithium development in the world:
Africa (https://news.pontemanalytics.com/p/illuminating-africas-path-from-energy)
Australia (https://news.pontemanalytics.com/p/what-a-flanker)
As a local entity in each region, with expertise in data, we think we are uniquely positioned to provide value in this space. Moreover, specific to Exxon’s DLE process, we found ourselves looking after drilling / completions, water injection, brine chemistry, etc., etc. (sound familiar, oil & gas folks?)
Maybe…just maybe…some of us at Pontem took a flyer on securing a chunk of underdeveloped acreage in Ouachita County, Arkansas some years ago in a dying basin called the Smackover…
Sir we should talk. I own land there and am following developments for pursuit of leases.
Feel free to email jtfujmw@gmail.com.