Background
In pipeline operations, tracking a pig—an essential device for liquid management, maintenance, and inspection—is critical for efficiency and safety. However, the task grows increasingly complex in long, multiphase pipelines as liquid content in the pipeline builds resistance against the pig, upstream flowrates can fluctuate, and downstream pressures can change. Simple calculations based on gas velocity often drastically under predict the actual pig time and thus lead to false impressions of when the pig will arrive.
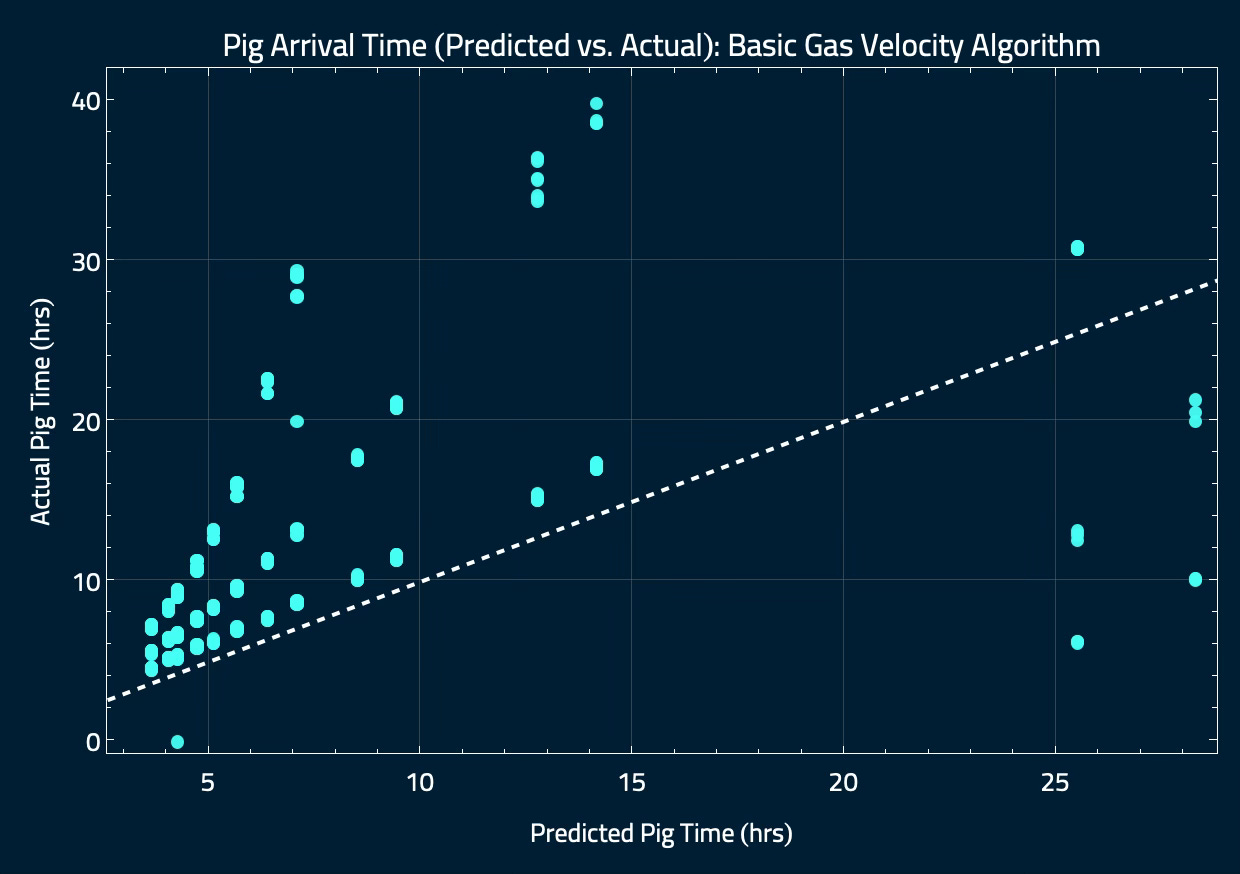
Recently, at Pontem, we collaborated with an operator experiencing a similar challenge: the inability to accurately predict the arrival time of a specific pig due to its extensive and undulating multiphase pipeline with varying production conditions during pigging.
This issue resulted in numerous operational challenges, primarily centered around managing the excessive liquids associated with pig arrival. While certain setup measures can be implemented to enhance liquid handling, adequate ‘heads up’ is necessary to avoid potential disruptions to typical processing when excess liquids are not present.
Typical Industry Solutions
The desire to track pigs and have a better understanding of when they will arrive is not a new request from operators. In fact, industry solutions to this problem have existed for quite some time.
However, most of these solutions leverage the use of online multiphase simulators, which are physics-based pieces of software installed within the companies IT infrastructure that simulate the pig travel in real-time. While these solutions can be accurate and useful, they often suffer from two major issues:
High Costs / Long Lead Times: Transient simulators require significant financial investment and often take many months to properly configure to a new system.
High Computational Resources: Running multiphase physics-based algorithms is typically complex and requires high amount of computation resources (as well as IP development from the vendor, in turn increasing the costs)
In this case, the issues with costs and long lead times were prohibitive for the operator and therefore a new solution was required.
Pontem’s Solution: A PIML-Driven Pigging Algorithm
To create an accurate pig tracking algorithm for the client in the most cost-effective manner possible, we implemented a physics-informed machine learning (PIML) algorithm tailored to their pipeline conditions. This innovative solution combined physics-based modeling with machine learning to dynamically adapt to real-time data.
Physics Informed Machine learning minimizes physics and data loss together
The algorithm’s key features included:
Real-World Complexity Modelling
The algorithm accounted for liquid holdup, fluctuating flow rates, and pipeline-specific undulations to provide precise pig tracking.Dynamic Adaptation to Flow Rate Changes
It adjusted to upstream and downstream variations in real time, ensuring consistent accuracy under changing conditions.Rapid Deployment and Integration
Deployment was achieved within weeks instead of months, leveraging the operator’s existing SCADA infrastructure via OPC UA protocols for seamless integration.Automated Learning and Continuous Refinement
The PIML model improved accuracy over time by continuously refining itself using real-time production data, reducing the need for manual recalibration.User-Friendly Dashboard
A dynamic dashboard provided live updates on pig location, velocity, and arrival times, as well as historical data for future optimization.
Results: Positive Outcomes for the Operator
The PIML-driven pigging algorithm delivered exceptional results. Operators have the ability to mark when the pig is inserted in the trunkline and then receive real-time pig location updates so they are prepared for when the pig will arrive.
To enable the real time updates and ensure its accuracy, the algorithm is integrated into the SCADA system, where it continuously reads upstream source rates and downstream pressures. Based on these keys inputs, the plot below shows how well the model performs, indicating a vast improvement over the simplified gas velocity calculations previously employed.
Pig arrival time comparison (above) and tracking application HMI (below)
Key Takeaways and Future Work
This operator's success story highlights how a PIML-driven solution can redefine pipeline pigging operations. The algorithm not only resolved immediate challenges but also provided a scalable, adaptable framework for future pipeline management needs.
By embracing innovative approaches like PIML, operators can ensure smarter, safer, and more efficient pipeline operations while significantly reducing costs and improving accuracy.
While initially designed for pig tracking, this PIML framework has the versatility to address a wide range of pipeline challenges, including risk-based hydrate management, wax deposition monitoring, liquid management in multiphase pipelines, and ongoing corrosion risk forecasting.
Embracing a PIML-driven framework transforms pipeline monitoring by delivering cost-effectiveness over previous approaches involving custom tailored physics-based software that is time consuming and expensive to create and deploy.
Stay tuned as we continue to refine and expand this technology, delivering exceptional value and operational excellence across the industry.