Case Study: Integrated Dynamic Modeling (OLGA / Hysys)
De-risking a subsea tieback with severe slugging potential
Background
In oil and gas fields, much like everyday life, you never know when opportunities will present themselves. It’s not uncommon for existing fields to discover new resources nearby that they would like to produce. Sometimes, these discoveries are substantial enough that entire new infrastructure is required, in which case a new design can be created. Other times, however, new production must be made to “work” inside the existing systems to make the economics favorable.
The latter case can generally carry a higher amount of risk because you aren’t as free to design the system from the ground up as you are when given a clean slate. At this point, the goal of any work is focused on turning that “risk” into a true “opportunity”.
Pontem has recently been involved in an offshore project currently producing a relatively lean gas condensate through a 50 kilometer tieback from an unmanned platform to a larger processing facility. When the discovery of oil nearby to the existing gas was made, it left the operator with no choice but to consider creative ways that it could be extracted and produced.
The projected oil recovery was insufficient to justify the expense of a new design and so the only hope of producing the oil was to use the existing system, co-producing the current gas and the prospective oil through the same subsea pipeline and processing equipment topsides.
There were numerous production chemistry challenges identified for the commingled gas/oil mixture that would be produced (we’ll save those for additional case studies). However, one of the primary concerns was how the current system would handle the increase in liquids resulting from the production, considering the system was originally designed to receive primarily gas with only small amounts of condensate.
A bit of “boring” theory….
Among the various flow regimes observed in multiphase flow, unstable (“slug”) flow represents a complex and dynamic behavior that poses significant challenges to production efficiency and system integrity. Slug flow is characterized by the intermittent passage of liquid slugs interspersed with gas pockets within the flowline. These slugs can vary in size, velocity, and composition, leading to fluctuations in pressure, flow rates, and fluid distribution along the pipeline. Potential impacts can be off-spec production, tripping set-points/alarms and shutting in production, fatigue / structural damage to pipe structures, and the need for large vessels.
The occurrence of unstable flow is influenced by a multitude of factors including flow rates, fluid properties, well geometry, and operating conditions. Understanding the mechanisms underlying slug flow is crucial for designing effective control and mitigation strategies. Two primary types of slugging commonly observed in oil and gas production are the terrain and hydrodynamic induced slugging.
Terrain or Riser Slugging (the “difficult” one) - Caused by the pipeline routing profile. Variations in elevation along the pipeline, such as hills or valleys, or the base of a riser, can lead to the accumulation of liquids in the low points under the influence of gravity. This accumulation can intermittently block the gas phase, causing slugs of liquid to be transported through the pipeline.
Hydrodynamic Slugging (the “easy” one) - Caused by the fluid dynamics, more specifically the interaction between the gas and liquid phased within the flow. Variations in flow rates, fluid properties, or pipeline conditions can lead to the formation of an unstable flow regime, causing the gas phase to intermittently accelerate and decelerate the liquid phase, forming slugs.
As a side note, Pontem personnel have actually visited numerous testing facilities where multiphase flow is studied. Here’s a neat look at real slugging, in this case from an apparatus designed to replicate flow in a horizontal lateral.
Back to the project
In order to grasp the system's dynamics and anticipate the behavior of the pipeline, we conducted multiphase hydraulic modeling spanning the project’s expected lifespan. This analysis aimed specifically at understanding the potential slugging phenomena that may occur within the pipeline and the resulting impact on liquids handling at the receiving facility.
And needless to say, the outcomes didn’t look good…
The plot below shows what the liquid arrival rates were expected to look like over various years. Considering that the current pipeline had been in place for some time and, by most accounts, is oversized for its current gas production, the addition of significant amounts of liquid in the line leads to increased holdup and ultimately drastic slugging behavior. When we showed this plot to the operators for the first time, that's when things really started to “get real”.
So what can go wrong in the case above? Well, the primary risk is that these slugs of liquid we see will come into the topsides facility at such a high rate and with so much volume, they will overwhelm the vessels that exist currently.
You can think about this like a bathtub, which has a certain volume, and more than likely the maximum flow possible from your faucet is about equal to how much you could simultaneously remove if your drain is completely open. But, what would happen if someone suddenly dumped the volume of a couple of sinks' worth of water into your tub all at once? You can start to see where this gets problematic quickly.
A quick screening
One of the ways we can “quickly” screen for problematic scenarios in handling liquid volumes is by calculating a surge volume as a function of various drain rates. In keeping with the bathtub analogy above, the idea is to take the liquids you see arriving at your vessel and then, for various “drain rates,” calculate how much excess volume would be needed in the vessel at any given point to match the surge in volume. This, in theory, tells you whether the volume you have in the existing vessel receiving the liquids is enough or whether it will exceed the capacity, which leads to flooding and shut-ins.
As expected based on our slugging plot, our analysis showed that several years in the profile would be problematic based on our current drain rate and vessel volume. In fact, with the current separator’s volume, we would need over 3x the drain rate than what exists currently.

If this were a project being designed from the start, we could simply look to either a) increase the inlet separator size or b) increase our drain rate, both of which would solve the problem. However, for an existing system already in place, neither of those options is easy, or rather, neither are obtained without significant cost. This is where a more rigorous analysis comes in, which can be the difference between the project moving forward or not.
A more detailed screening
The methods of screening liquids handling issues mentioned above are good but are generally conservative. For example, they don’t take into account any flexibility of the equipment to scale up or down through the control system to temporarily accommodate slugs. And when the success of the project depends on the ability to make the existing equipment work, ensuring whether we can or can't accommodate the slugs is crucial.
The tools utilized to simulate the subsea pipeline and predict the slugging behavior (software like OLGA and Ledaflow) are not the best suited for modeling the intricate details of process equipment as outlined in the PFD of the existing topsides shown below. That is best done by software tools like HYSYS and Symmetry, which specialize in modeling such details.
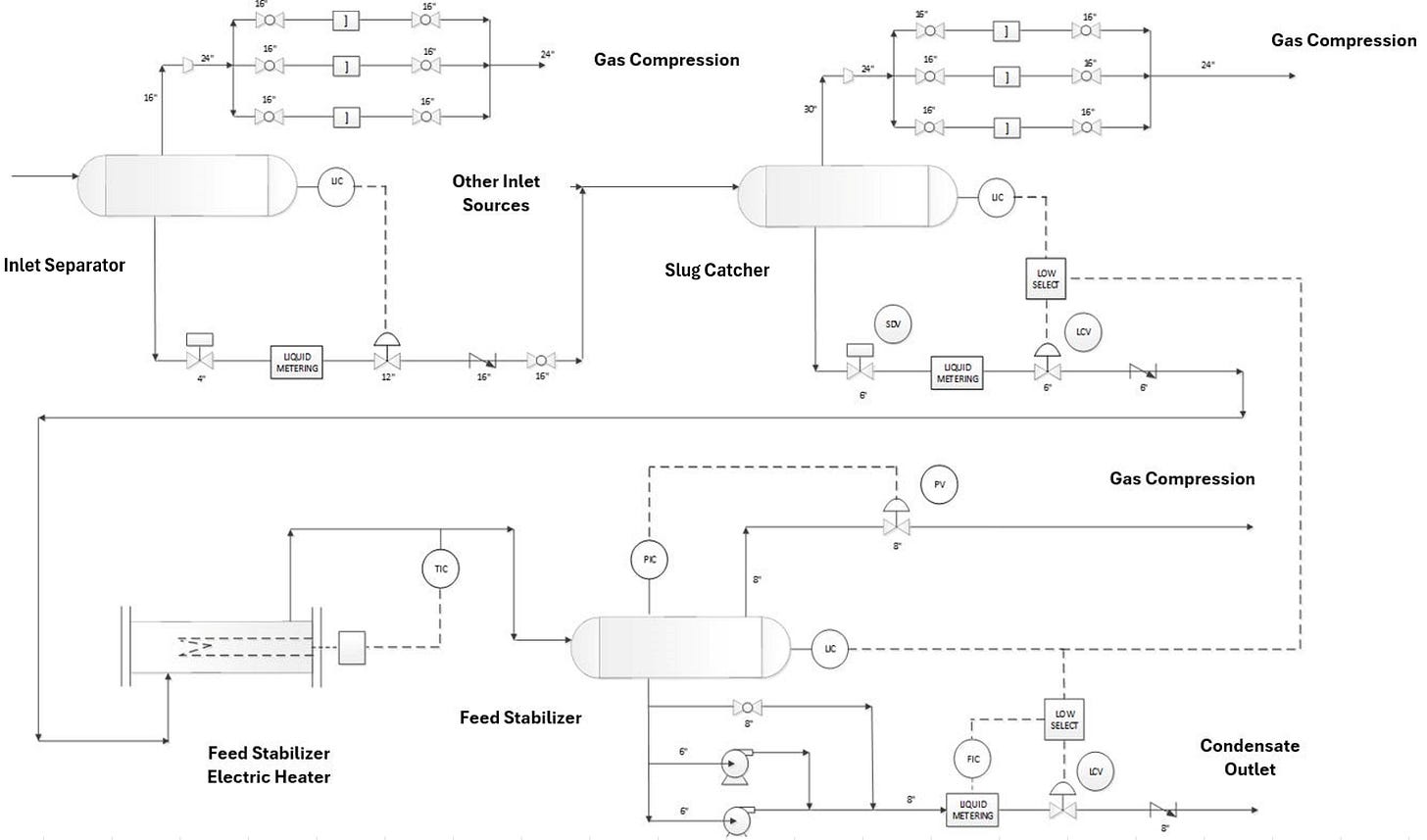
Fortunately, there are emerging tools and links available that allow some of these crucial software programs to communicate with each other, unlocking the best of both worlds, and Pontem has quite a lot of experience with them.
So, after building the topsides process model (in Hysys in this case), we connected it to the existing subsea pipeline model (which was created in OLGA). After doing so, we were able to let the liquid slugs predicted by the pipeline model feed directly into the process model to see how the entire system responds.
Some of our initial findings indicated potential issues. The inlet separator could successfully drain the liquid surges. However, the further downstream slug catcher, which also receives liquids from other fields that produce to this facility, couldn’t keep up. As a result, we observed liquid levels continually rising as more slugs were produced indicating a situation that wasn’t sustainable.
Ultimately, this led to further discussions with the existing operator of the topsides facility around their control logic and what we could do to improve it. With a few modifications and upgrades in their existing control philosophy, we were able to show that the liquid slugs being received COULD successfully be handled with the existing equipment throughout the entire life of the field.
Clearly, this was a huge win for the project by de-risking the production aspects and enabling the use of existing facilities, and without major modifications. This offers an economically-attractive alternative, even if the design isn’t truly “optimized”. As with most brownfield developments, good enough might be…well…good enough. The project itself still has other challenges that it faces. However, now that we know handling the slugs we see is possible through detailed and integrated flow modeling, it’s a big sigh of relief for one of the most pressing challenges.
Wrapping up
It would be very easy after some of the earlier work done on this asset to throw our hands up and conclude that producing the oil in the existing system was just too problematic and risky. It would certainly be the safe option.
But, being able to investigate this on a much deeper and more detailed level by combining multiple pieces of software, each with their own areas of expertise, we can gain a better understanding of how the system would perform, ultimately leading to de-risking it.
In this case, that understanding was the difference between allowing the project to continue as opposed to being shutdown.
"Things are not always what they seem; the first appearance deceives many." - Phaedrus